Ncore ERP is an enterprise resource planning (ERP) software solution designed to integrate core business processes such as finance, HR, supply chain, and manufacturing into a single system. This case study explores how Plasto, a mid-sized manufacturing firm, utilized Ncore ERP to enhance operational efficiency, optimize resource utilization, and drive business growth.
Company Overview: Plasto is a leading manufacturer of plastic bags with operations spread across multiple locations. With a diverse product portfolio and complex supply chain requirements, the company faced challenges in managing inventory, coordinating production schedules, and ensuring timely delivery to customers.
Challenges Faced:
- Disparate Systems: Company Plasto relied on disparate systems for managing various business functions, leading to data silos, inefficiencies, and inaccuracies.
- Inventory Management: Inaccurate inventory tracking resulted in stockouts, excess inventory, and increased carrying costs.
- Production Planning: Manual production planning processes led to suboptimal resource allocation, production delays, and increased lead times.
- Compliance: Ensuring compliance with industry regulations and quality standards was a time-consuming and error-prone process.
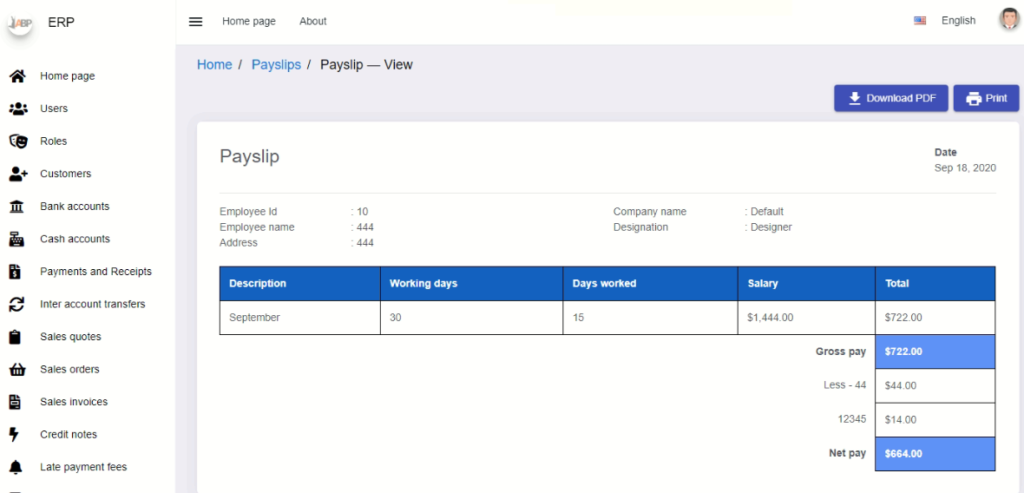
Implementation of Ncore ERP: Company Plasto decided to implement Ncore ERP to streamline its operations and address the challenges faced. The implementation process involved the following steps:
- Assessment and Planning: Conducted a thorough assessment of existing processes and identified key areas for improvement. Developed a comprehensive implementation plan outlining objectives, timelines, and resource requirements. We selected Technologies as per the needs of the system depending on speed, productivity, demographics, user-friendliness etc.
- Customization and Integration: Customized the Ncore ERP solution to align with Company Plasto’s unique business requirements. Integrated the ERP system with existing third-party applications and legacy systems to ensure seamless data exchange.
- Training and Change Management: Provided comprehensive training to employees on using the new ERP system effectively. Implemented change management strategies to facilitate smooth transition and minimize resistance to change.
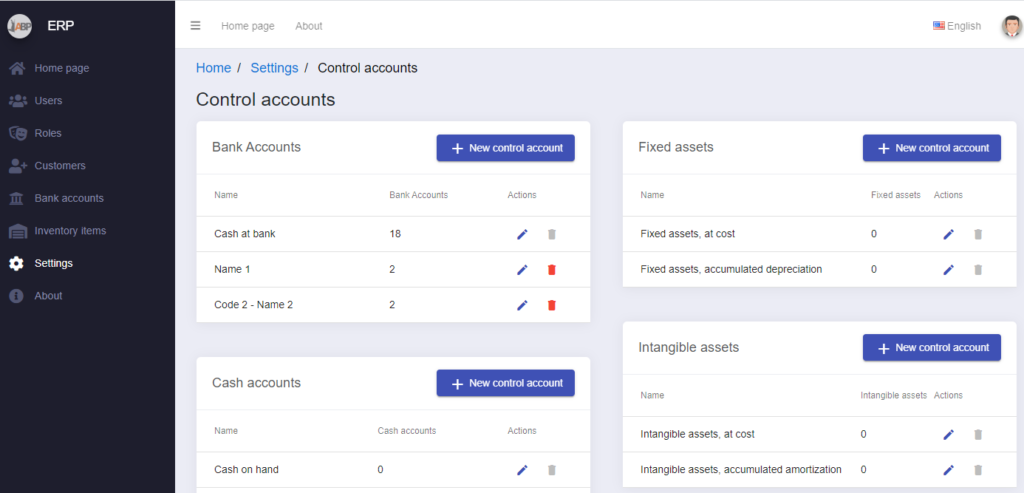
Features in Ncore ERP:
– Payment & Receipts
– Sales Orders & Invoices
-Credit Notes/Debit Notes
– Warehouse Management
– Financial Dashboard
– CRM
– Purchase Orders & Invoices
– Inventory Management
– HRMS/Payroll
– Reports
– Assets/Capital Account etc.
– Tax Codes/ Chart of Accounts.
– Trial Balance/Amortization entries/Journal entries etc.
Benefits Realized:
- Streamlined Operations: Ncore ERP enabled Plasto to streamline its business processes, eliminate redundancies, and improve cross-departmental collaboration.
- Enhanced Inventory Management: Real-time visibility into inventory levels and automated replenishment processes helped Plasto optimize inventory levels, reduce stockouts, and lower carrying costs.
- Improved Production Planning: Advanced planning and scheduling capabilities of Ncore ERP enabled Plasto to optimize resource utilization, minimize production lead times, and meet customer demand more effectively.
- Enhanced Compliance: Ncore ERP’s built-in compliance features and real-time monitoring capabilities helped Plasto ensure adherence to industry regulations and quality standards, reducing the risk of non-compliance.
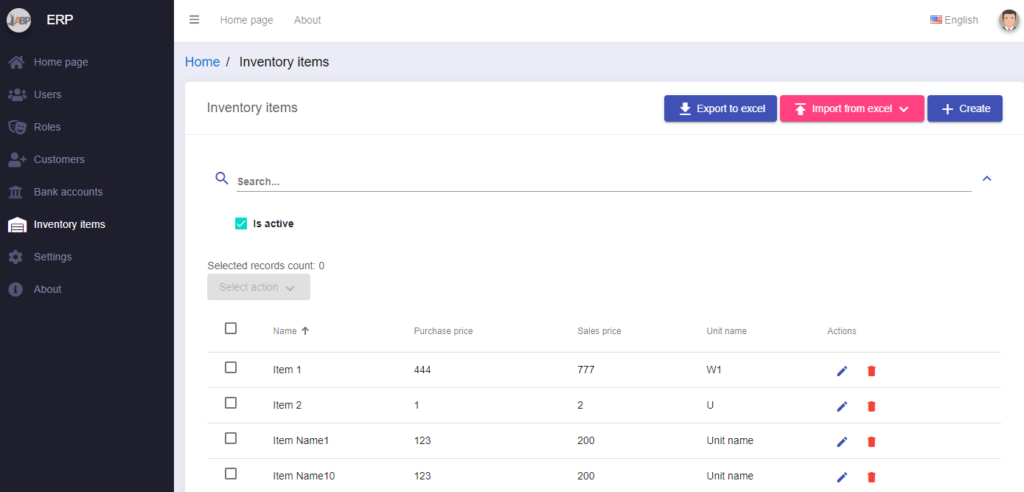
By leveraging Ncore ERP, Plasto was able to overcome operational challenges, improve efficiency, and drive business growth. The centralized platform provided real-time visibility and control, enabling better decision-making and strategic planning. Moving forward, Plasto continues to harness the power of Ncore ERP to stay competitive in a rapidly evolving market landscape.